Recognizing the Trick Parts and Repair Work Techniques for Packaging Equipment Upkeep
Effective upkeep of product packaging devices pivots on a comprehensive understanding of their crucial parts, including the framework, drive system, and securing devices. Recognizing typical upkeep concerns, coupled with the application of preventative approaches and troubleshooting methods, can dramatically enhance maker integrity.
Key Elements of Packaging Machines
Packaging makers are composed of a number of vital components that collaborate to guarantee effective and efficient product packaging procedures. At the core of these equipments is the structure, which provides structural integrity and houses the various operating parts. The drive system, frequently a combination of gears and motors, facilitates the movement of components, enabling accurate operation throughout the packaging cycle.
One more vital element is the conveyor system, which moves products via various phases of the product packaging process. This is typically matched by sensing units and controls that check the placement and rate of products, making sure synchronization and lessening mistakes. The loading system is critical for accurately giving the ideal quantity of item into packages, whether in liquid, powder, or solid kind.
Sealing mechanisms, consisting of warm sealers or glue applicators, play an essential function in securing plans, stopping contamination and prolonging life span. Furthermore, labeling systems are indispensable for supplying needed product details, making sure compliance with laws. Lastly, the control panel, outfitted with easy to use user interfaces, enables drivers to handle machine features, monitor performance, and make changes as needed, making certain ideal performance and effectiveness in product packaging operations.
Common Upkeep Concerns
Effective operation of product packaging machines relies greatly on normal upkeep to stop typical concerns that can disrupt production. Amongst these concerns, mechanical wear and tear is prevalent, especially in parts like conveyors, seals, and motors, which can result in unanticipated downtimes. In addition, misalignment of parts can lead to ineffective procedure, creating items to be inaccurately packaged or damaged during the process.
One more typical upkeep concern entails the build-up of dust and particles, which can hinder the machine's sensing units and moving components. packaging machine repair service. This not only impacts efficiency however can likewise posture safety and security threats. Furthermore, lubrication failings can lead to enhanced friction, resulting in overheating and eventual part failing.
Electric troubles, usually originating from loosened links or worn-out wiring, can interrupt equipment features, causing considerable manufacturing delays. Finally, software application glitches as a result of obsolete programs or inappropriate arrangements can prevent the equipment's procedure, requiring immediate treatment. Addressing these common maintenance issues proactively is vital for ensuring optimum efficiency and durability of product packaging equipment.
Preventative Upkeep Methods
Carrying out preventative maintenance techniques is important for maintaining the effectiveness and reliability of packaging devices. These techniques include a methodical approach to upkeep, concentrating on the regular examination and servicing of devices to preempt potential failures. By sticking to a set up maintenance program, drivers can identify deterioration on parts before they cause substantial break downs.
Trick elements of a preventative maintenance method consist of routine assessments, part, lubrication, and cleaning replacements based upon manufacturer suggestions. Using lists can streamline this process, making certain that no important jobs are forgotten. In addition, maintaining accurate records of maintenance activities help in tracking the equipment's performance in time, assisting in informed decision-making pertaining to future upkeep demands.
Educating team on the relevance of preventative upkeep boosts conformity and cultivates a society of aggressive treatment. Implementing a predictive maintenance part, making use of data analytics and sensing unit technology, can further optimize equipment efficiency by forecasting failings prior to they occur.
Repairing Methods
When faced with malfunctions Read More Here or inadequacies in product packaging makers, employing systematic troubleshooting strategies is necessary for determining and dealing with issues promptly. The very first step in reliable troubleshooting is to develop a clear understanding of the device's functional specifications and performance metrics. This includes examining the maker's requirements, as well as any type of mistake signals or codes presented.
Next, operators should perform a visual assessment, looking for apparent indicators of imbalance, damage, or wear. This frequently consists of examining gears, belts, and sensors to identify possible root causes of malfunction. Collecting functional data, such as production prices and downtime logs, can additionally offer understandings right into repeating problems.
As soon as prospective problems are determined, making use of a logical method to separate the source is essential. This might call for screening individual components or systems in a controlled fashion. Participating in discussions with operators who engage with the equipment routinely can produce useful responses concerning uncommon behaviors or patterns.
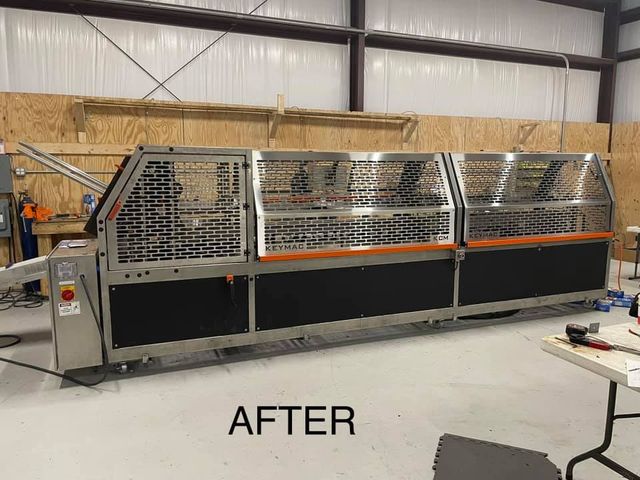
Repair Work and Replacement Ideal Practices
A thorough understanding of repair service and replacement best techniques is crucial for preserving the longevity and performance of packaging machines. Regularly analyzing the condition of device parts enables for timely treatment, stopping more substantial concerns that can result in expensive downtimes.
When fixings are essential, it is important to utilize OEM (Original Tools Maker) parts to make sure compatibility and performance. This not just preserves the stability of the machine yet also maintains warranty contracts. In addition, it is recommended to keep an inventory of essential spare components to facilitate quick substitutes and minimize operational disturbances.
For complex repair services, involving certified service technicians with specialized training in product packaging machinery is suggested. They have the knowledge image source to detect issues accurately and carry out fixings efficiently. Documenting all repair work activities and components substitutes is crucial for preserving a thorough upkeep background, Get More Info which can assist in future troubleshooting.
Last but not least, implementing a proactive method, consisting of routine examinations and anticipating upkeep strategies, boosts the integrity of product packaging equipments. By sticking to these ideal techniques, organizations can ensure optimum equipment efficiency, minimize functional dangers, and prolong devices lifespan.

Conclusion
In conclusion, a complete understanding of packaging equipment components and effective maintenance approaches is crucial for ideal efficiency. By executing these practices, organizations can make sure the long life and efficiency of packaging devices, eventually adding to boosted functional performance and lowered costs (packaging machine repair service).
Reliable upkeep of product packaging machines hinges on an extensive understanding of their crucial elements, including the framework, drive system, and sealing systems.Efficient operation of packaging devices relies heavily on regular upkeep to protect against usual concerns that can interfere with manufacturing.Carrying out preventative upkeep methods is important for sustaining the performance and dependability of packaging devices. Additionally, maintaining exact documents of maintenance activities aids in tracking the equipment's efficiency over time, assisting in notified decision-making concerning future maintenance demands.
